Trunnel experiments
I got the black locust this weekend. Nice stuff, golden yellow, and very heavy. Jeremy at CWB was kind enough to spend a few minutes on the tablesaw for me cutting them into the ~3/8x3/8" squared, that are then pounded through the dye to make the round trunnels.

And now begins the trunnel width to bore diameter dilemma. Its basically trying to make sure that the trunnels are wide enough in the hold to fit snugly and hold their grip (necessary for it to be a fastening) but not too snug, or they will just crack and break while trying to pound them in. The dye plate has holes from 3/8" to 7/16" in 1/64th increments. Add to this the irregularities in bored hole diameter between high-speed twist bits, forstner bits, and brad point bits. The former makes the largest hole, the latter making the tightest, or most precise to the claimed diameter on the bit (from my experiments).
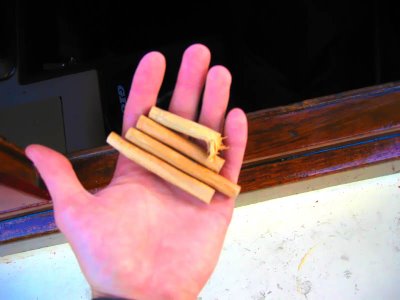
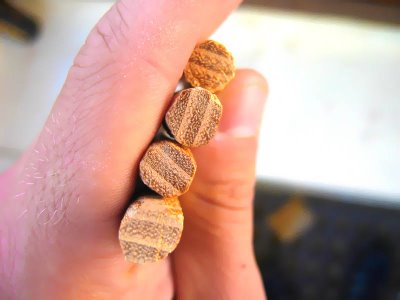
It looks like the second to largest hole in the dye combined with the brad point drill bit makes a really snug fit without breaking the trunnels too much. But in the smaller test bits I used, they split the wood really easily. I wanted to practice on a full size piece of wood, but I didn't want to sacrifice any of the good, large bits I have. So I practiced on the dock (I hope my marina manager is not reading this...). That's how I came up with the seemingly right combo.


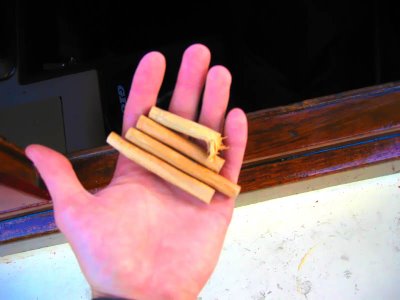
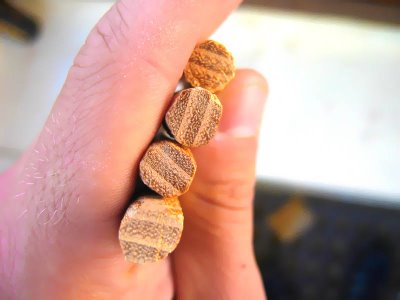
It looks like the second to largest hole in the dye combined with the brad point drill bit makes a really snug fit without breaking the trunnels too much. But in the smaller test bits I used, they split the wood really easily. I wanted to practice on a full size piece of wood, but I didn't want to sacrifice any of the good, large bits I have. So I practiced on the dock (I hope my marina manager is not reading this...). That's how I came up with the seemingly right combo.

0 Comments:
Post a Comment
<< Home