Installing graving pieces
I tried two times to pilot holes through the block and the frame so that I could use screws to hold the bits in while the epoxy was curing, but I could never get it to sit right with the screw cranked on. I wanted/needed it to get sucked up against the plank. So I went with my original idea of wedging them in at the seam, while pushing with my hand to keep it against the frame. Seems to work well. But in hindsight, I would have placed a sheet of waxed paper between the wedges and the block... but oh well...
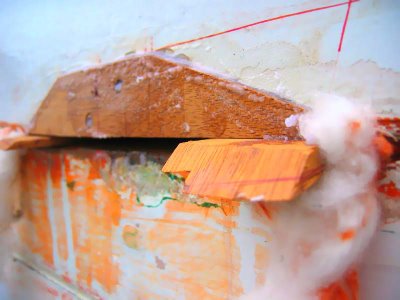

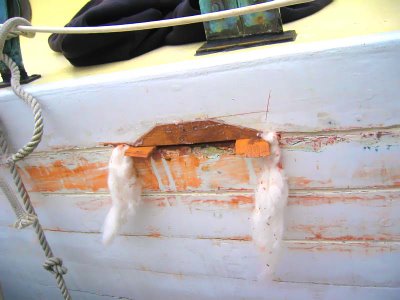
The whole thing was rather stressful, I don't particularly like using epoxy. I'm afraid that I didn't do it right and I'm going to spend weeks trying to chisel out my mistake.
Me being stressed:

In other news, the rain came again... finally. But the boat held up well and there was very little water in the bildge, even though there are a number of things I know should be fixed. So, that's a good omen for the boat when the real rain comes.